
-
Application Stories
• Building
• Furnace and Boiler Tube Inspection
• Medical
Shell Oil Refinery
Tracing Gas Leaks: Maintenance and Safety Problems Highlighted
With more than 160,000 kilometres of piping of every imaginable kind, Shell Nederland Raffinaderij in Pernis (Rotterdam) is the largest oil refinery in Europe. Safety and environmental considerations are firmly embedded throughout the company, its quality systems and its production management processes. Shell has also adopted a stringent safety policy in which preventive maintenance is uppermost.
Many chemical compounds and gases are invisible to the naked eye. Yet many companies work intensively with these substances before, during and after their production processes. Strict regulations govern how companies are to trace, document, rectify and report any leaks of volatile gaseous compounds, and how often these procedures are to be carried out. The most commonly used technology is the 'ToxicVaporAnalyzer (TVA) or 'sniffer technology'. "When searching for potential gas leaks, we check all systems at points that may or may not have been identified beforehand. These checks are carried out regularly, and are particularly important following a shutdown. At a refinery like the one we have here, this means carrying out tens of thousands tests on piping, stopcocks, seals, valves, torches, etc. Before we had the FLIR GasFindIR, an inspector using the TVA could carry out around five hundred inspections per day. An inspector using this infrared camera system can, on the other hand, get through an inspection regime of more than one hundred objects an hour. The most important reason for using the system is to minimise discharges of gas and other volatile organic substances from our pipework, particularly (potential) leaks around flanges and other gaskets", explains Rutger Zoutewelle, research analyst at Shell Pernis.
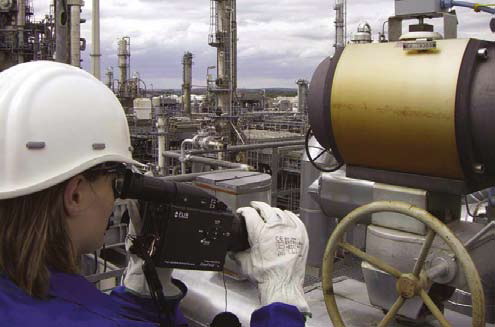
Inspector using FLIR GasFindIR to detect any and all irregularities and/or leaks.
- Home
- |
- Products
- |
- Training
- |
- Application |
- Image Gallery |
- Contact Us
Copyright ©2012 - Thermoscan Co., Ltd. - All Rights Reserved.
Thermoscan Co., Ltd. (บริษัท เทอร์โมสแกน จำกัด)
731 PM Tower, 5th Floor, Asok Dindaeng Road, Dindaeng, Dindaeng, Bangkok 10400
Tel: (02) 642-9489 Fax: (02) 642-9424
E-mail: tms@thermoscan.co.th